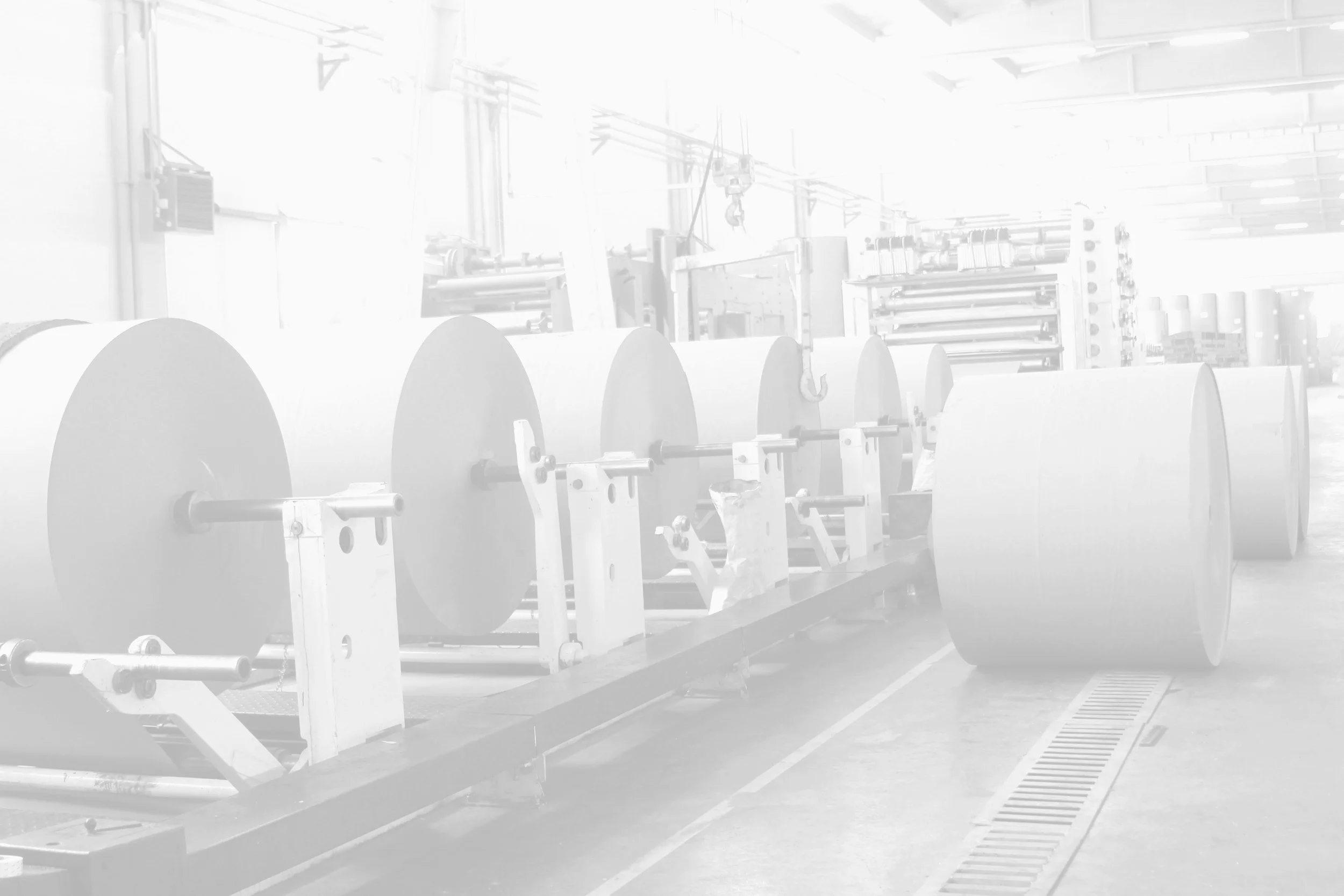
ECS is a software and hardware company with one goal in mind – to increase the realized capacity of your manufacturing process.
Our camera based quality control systems help increase the speed of the process while decreasing waste (defects and wasted material during process disruptions) and delay (downtime). Maintaining and increasing the realized capacity is not an option for today’s industries – it’s the key to survival and this task is not getting easier.
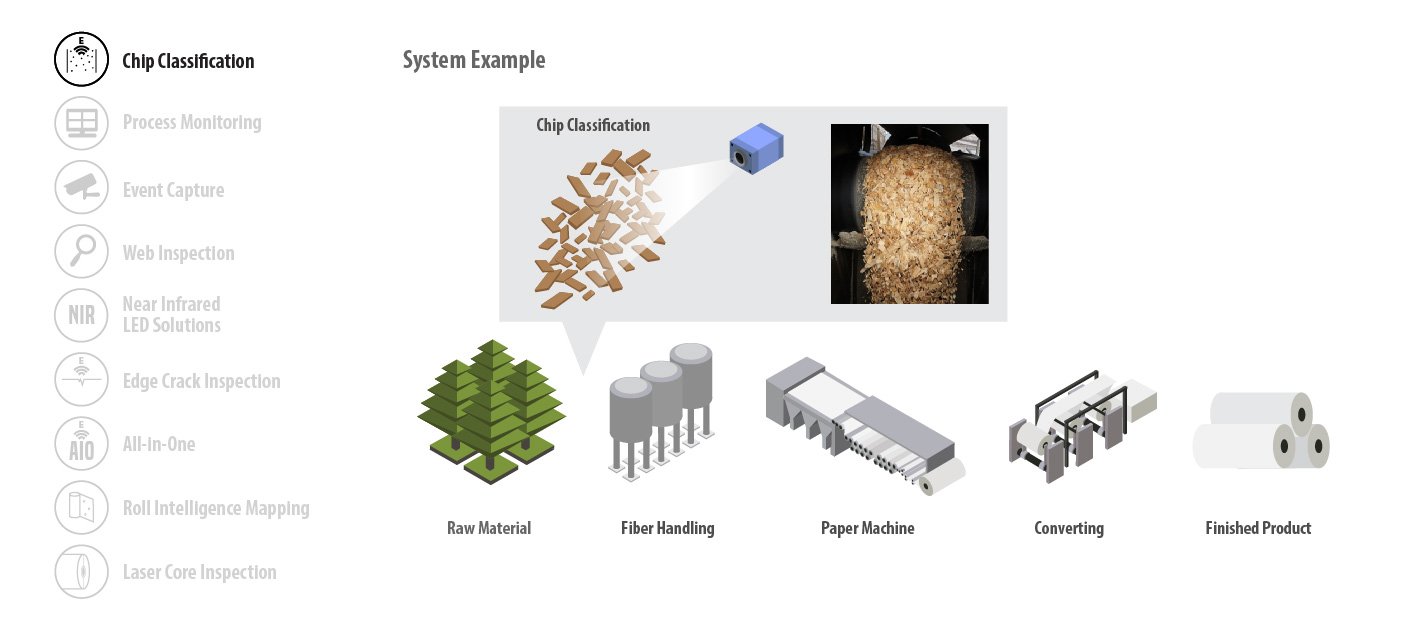
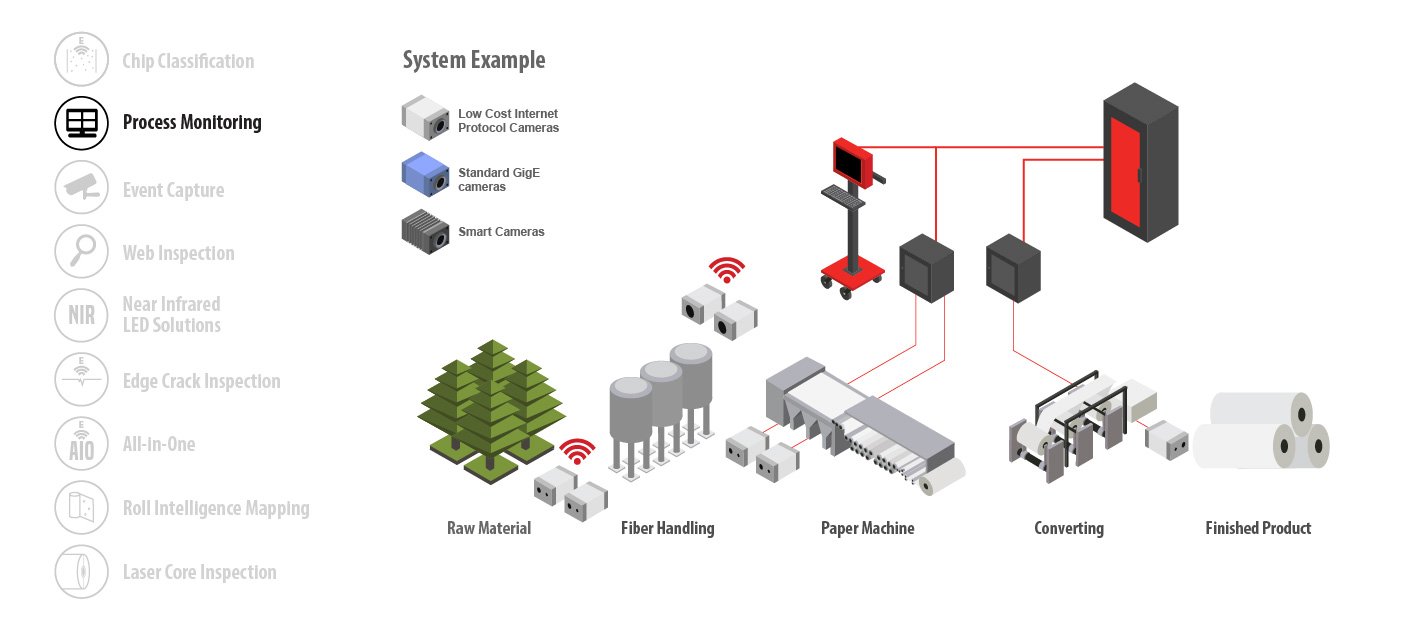

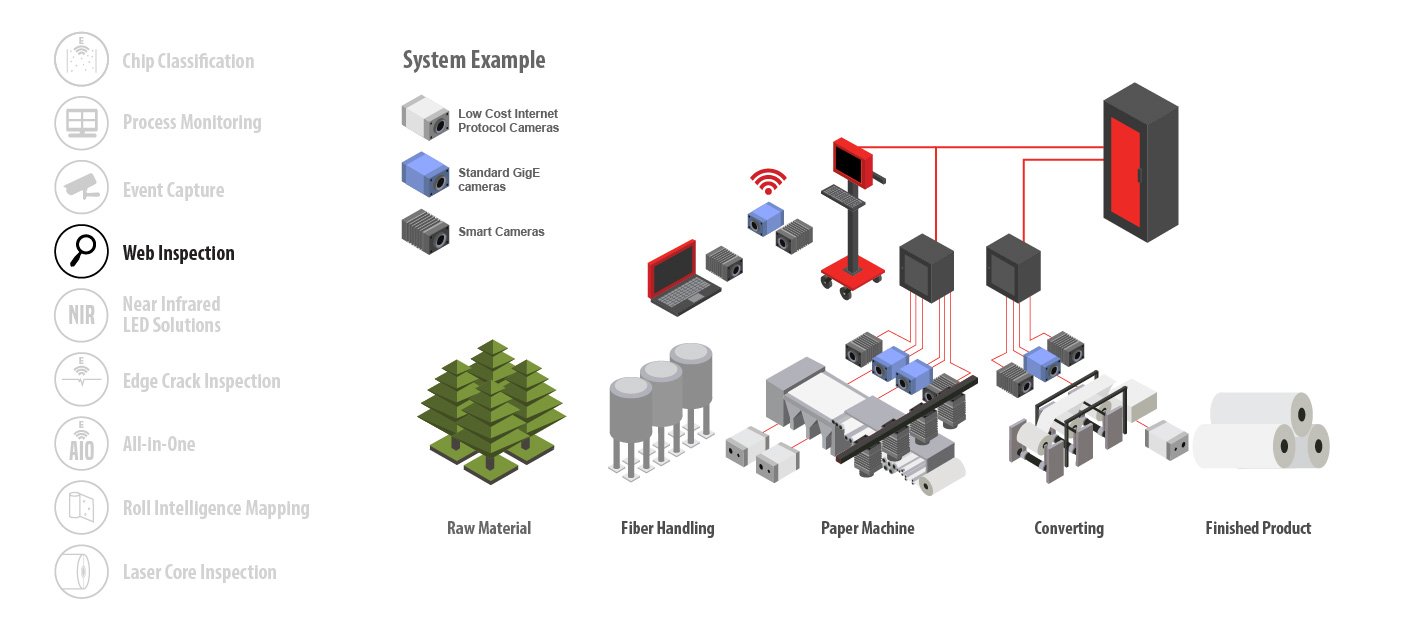
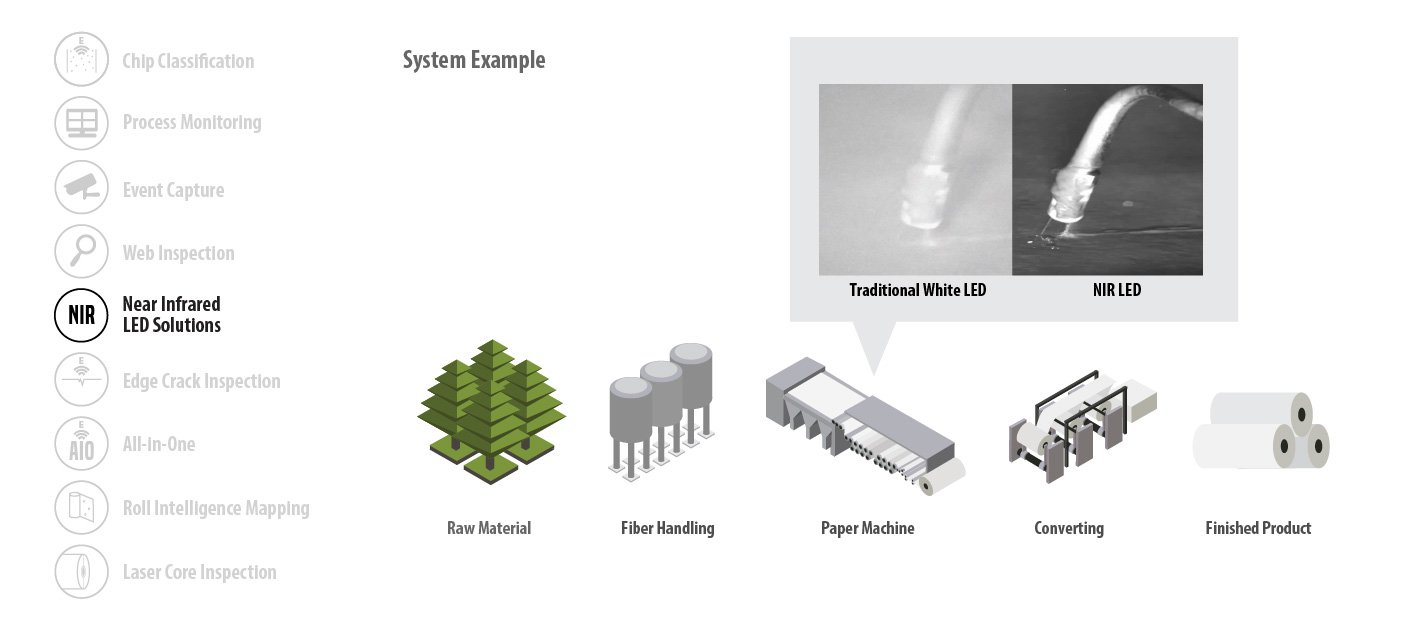
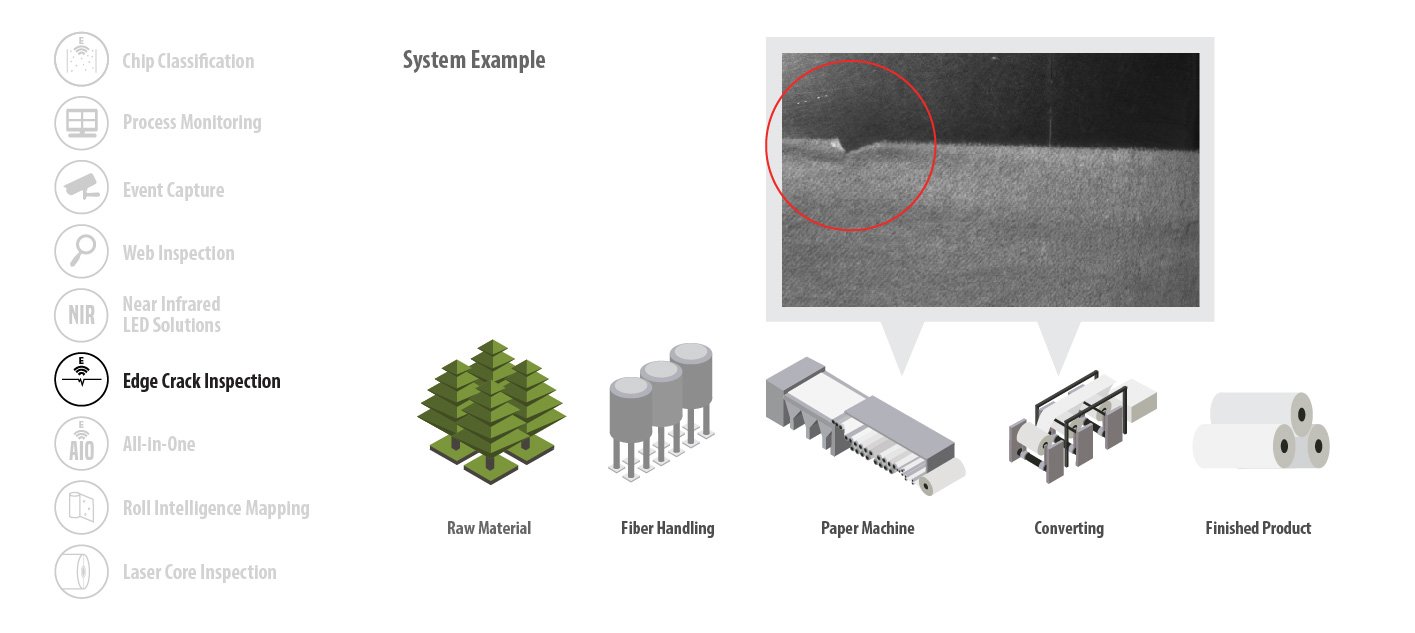
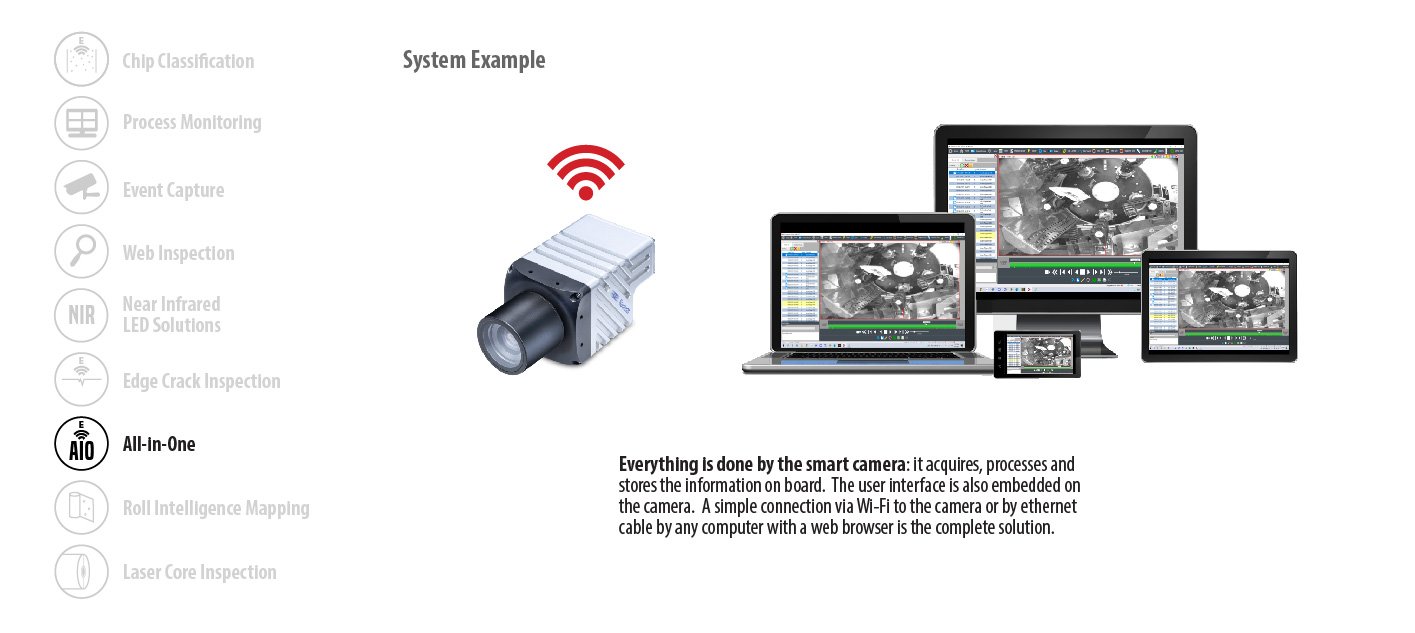
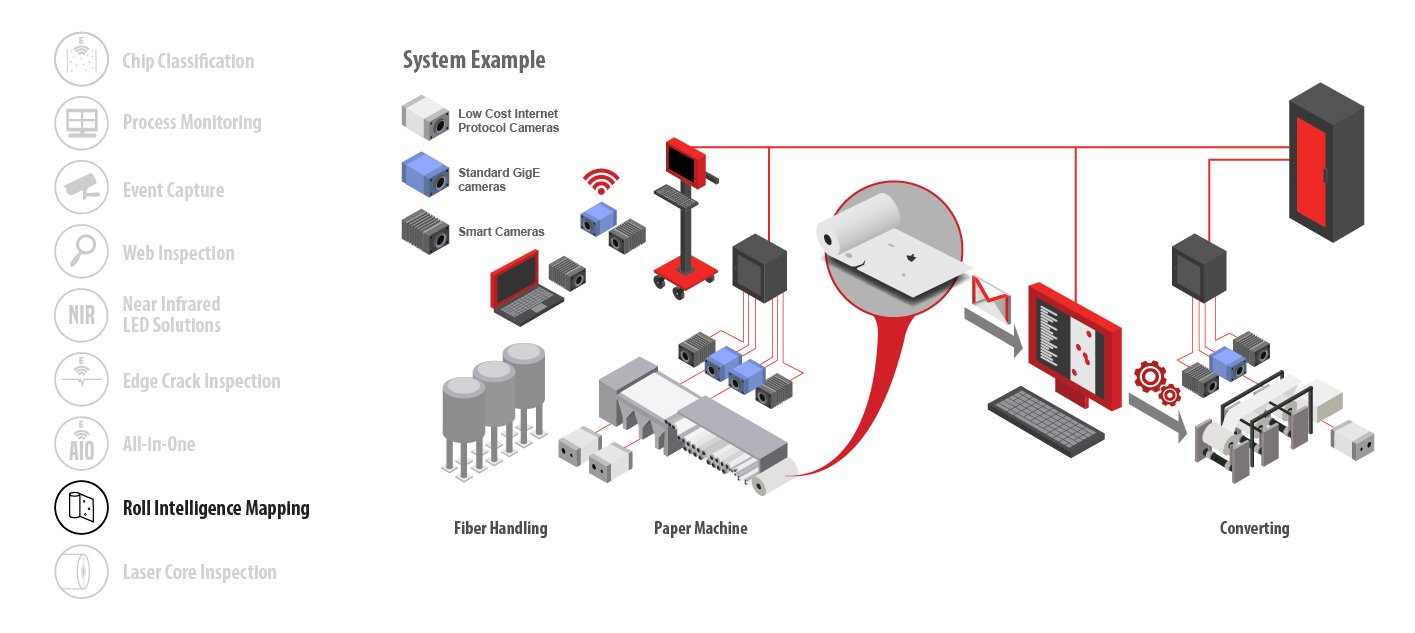
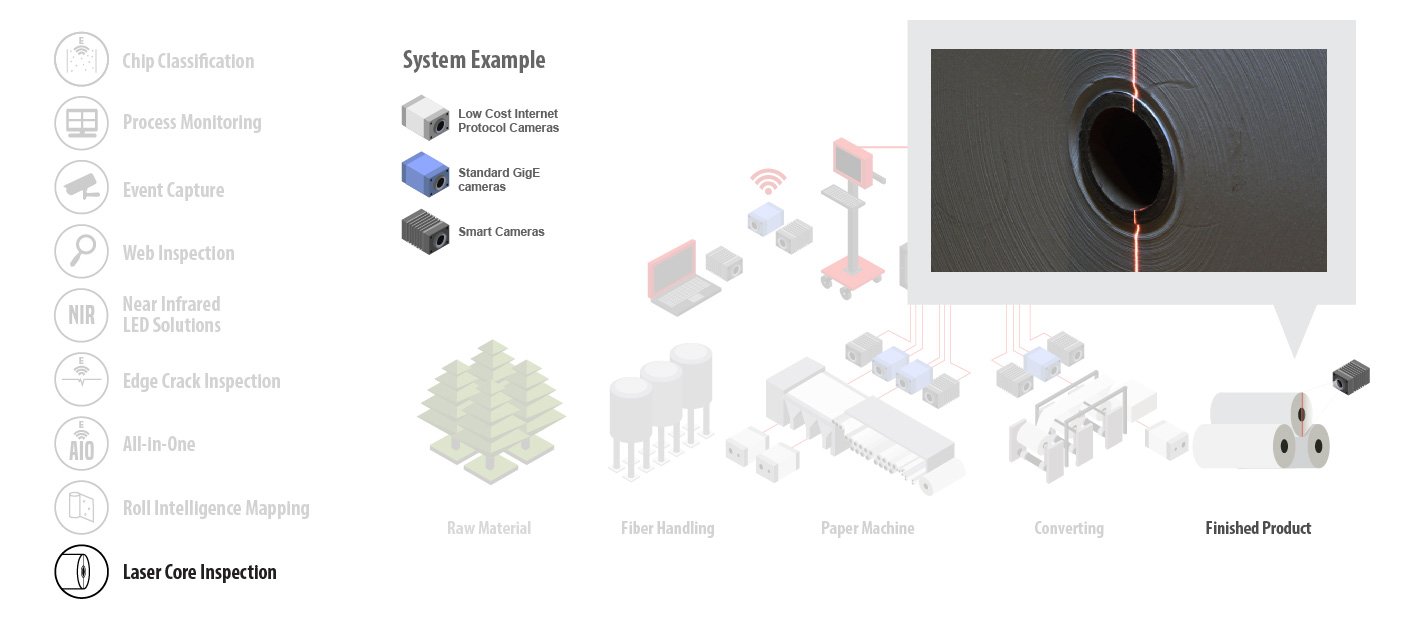
Why choose ECS?
Because these solutions become such a long-term and integral and critical aspect of best practices for our installed base – ECS understands we must become a partner in all aspects of the product lifecycle of these camera based solutions. We must be focused at all times on not only on how our systems are developed and built – but equally as important is the quality of installation and support. Our systems cannot afford to fail the operator and management when it’s needed most. In other words – we help increase uptime of your process – so the uptime of the camera based quality control system should never the problem.
The best equipment coupled with the best people.
REALIZED CAPACITY
From a solution standpoint – ECS provides a wide selection of quality control solutions under three main groups that can be installed in two ways
1. On a single process
a. Process Monitoring
b. Event Capture
c. Web Inspection
2. On a group of processes - RIM
Any of the solutions can be executed in the field from large permanent systems to small rolling or handheld configurations.
Is the basis of our system platform
Covered by 24/7 customer service
Chip Classification
HOW DEEP LEARNING IS USED TO INCREASE THE QUALITY CONTROL OF WOOD CHIPS BY CLASSIFICATION
An online and real-time camera-based inspection system positioned to monitor the wood chips from an incoming source can provide a breakdown of key wood chip parameters per time unit
Based on the time of inspection, the resulting classification can be tied back to the supplier (external or internal)
The mill can benchmark the actual chip quality parameter against set quality standards to determine corrective actions to provide optimum outcome of this raw material as it becomes paper
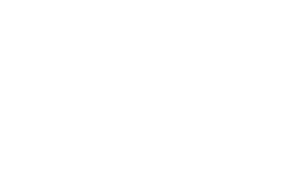
Process Monitoring
THE MOST ECONOMICAL WAY TO ADD VISIBILITY INTO HARD-TO-SEE AND DANGEROUS AREAS OF YOUR PROCESS
Uses Power over Ethernet IP (Internet Protocol) cameras
Camera signal can be sent via mill network or dedicated ECS camera network
High compression H264 video format to minimize burden on mill network
EVENT CAPTURE
A SCALABLE, INTUITIVE, TOUCH SCREEN SOLUTION FOR EVENT CAPTURE THAT CAN RUN ON ANY DEVICE
Multiple camera support with global synchronization
Ease of use in any environment - touch screen interface with industry standard screen gestures
Video image processing that can provide proactive indications of process faults, variations and defects
Completely non-proprietary hardware to support GigE camera video capture
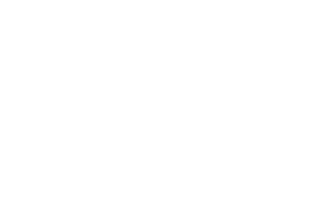
Web Inspection
OUR SOLUTION CAN IDENTIFY PROCESS DEFECTS IN HARSH CONDITIONS, AMBIENT LIGHT, OR MICRO WRINKLES WITH DEDICATED LED AND CAMERA BEAM CONFIGURATIONS
Utilizes area scan cameras for superior image quality
Directional analysis for web inspection in dusty environments
Single interface can show and control multiple beams along the machine direction on the same process
Web inspection data can be collected with additional process data on a per roll basis, and stored in the ECS process database
NIR LED
TAKE ADVANTAGE OF NEAR INFRARED (NIR) LIGHT TECHNOLOGY AND EMPOWER YOUR CAMERA TO SEE MORE WITH UNPRECEDENTED CLARITY
Clarity through the toughest steamy environments. NIR’s longer wavelength allows the light energy to penetrate the water vapor, hit the sheet and reflect back to the camera sensor.
See more without distractions. Reflected NIR energy from metal surfaces is less blinding to the camera sensor than reflected white light.
Make more visible to the camera. Because NIR is monochromatic it strips the color element out of the reflected light energy from the image.
Micro-pulsed NIR. The short on-time of the NIR LED creates exceptional stop action clarity even with the camera operating at ‘open’ shutter’
Wet line tracking. NIR lighting supports image processing programs that determine the positioning of wet lines along several parallel zones on the scene
Traditional White LED
ECS NIR LED
Edge Crack Inspection
SMART CAMERA SOLUTION WHERE ALL IMAGE ACQUISITION AND PROCESSING IS DONE ONBOARD THE CAMERA
No moving parts with camera-based, real-time edge tracking
Web Based Operator Interface – any computer can access the data and host the playback experience
Wi-Fi Capable to eliminate costly cable runs from camera to operator interface location
Auto Suspend Image Processing logic to eliminate need for any connection to the sheet break system
One-sided image acquisition (does not require a jaw design or any exposed sheet)
Ideal for Tissue Installations where there is no exposed sheet
System can run against a foil
All-in-one
THE ECS SMART CAMERA IS THE FOUNDATION OF THIS SOLUTION. EVERYTHING IS DONE BY THE CAMERA: IT ACQUIRES, PROCESSES, AND STORES THE INFORMATION ON BOARD
The user interface is also embedded on the camera
A simple connection via Wi-Fi to the camera or by ethernet cable by any computer with a web browser is the complete solution
Monitor, record, buffer, input external trigger and playback high speed frame by frame video is ready to go
Export video and images to share data
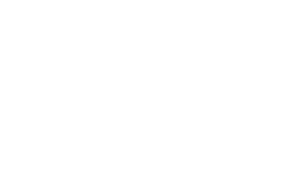
ROLL INTELLIGENCE MAPPING (RIM)
USING ECS INCREASES YOUR OVERALL EQUIPMENT EFFECTIVENESS (OEE) BY TRACKING PROCESS CHARACTERISTICS FROM THE PRIMARY ASSET THROUGH VALUE ADD CONVERTING
Web Inspection defect roll map for review and downstream machine control
Time stamp (sheet mark) the product during manufacturing
Read the mark at converting to provide proactive information on sheet quality
Correlate any process variable by time stamp from primary asset through converting
For example – a diaper starts from a rolled product 3 to 10 meters wide weighing several tons and is converted over multiple steps to create the highly engineered product used in a household. The overall realized capacity is a sum of the individual steps. RIM is the application of defect data from one process that is passed to the next process allowing these subsequent processes to optimize how it’s converted. A chain is only as strong as each individual link – RIM ensures each link in a multi-step process positively contributes to the overall realized capacity of the entire manufacturing cycle.
Laser Core Inspection
DETERMINE THE 2-DIMENSIONAL PROFILE OF THE CORE AND SURROUNDING ROLL BUILD TO DETERMINE IF THERE ARE PROTRUSIONS OR BASINS WITH 99.9% ACCURACY
Able to be installed with a wide range of different mill configurations (working distance, field of view, space for equipment)
High value and low cost of implementation
Low total cost of ownership in terms of installation and long-term maintenance
100% uptime
Small footprint
Seamless integration to mill information systems
Operator friendly with 24/7 dedicated customer support
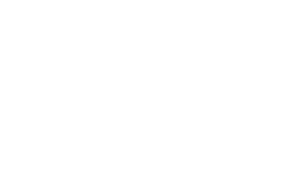