
EDGE INSPECTION MADE EASY
Smart Camera Solution where all image acquisition and processing is done onboard the camera
No moving parts with camera-based, real-time edge tracking
Web Based Operator Interface – any computer can access the data and host the playback experience
Wi-Fi Capable to eliminate costly cable runs from camera to operator interface location
Auto Suspend Image Processing logic to eliminate need for any connection to sheet break system
One-sided image acquisition (does not require a jaw design or any exposed sheet)
Ideal for Tissue Installations where there is no exposed sheet
System can run against a foil
Download the Edge Inspection info sheet below
WHY Edge Crack Inspection matters
Edge crack issues are costly downtime events for all grades of paper manufacture. Edge cracks can cause paper breaks on the paper machines.
Worse – edge cracks that do not break the sheet at the paper machine can cause downtime on more value-add and downstream converting operations.
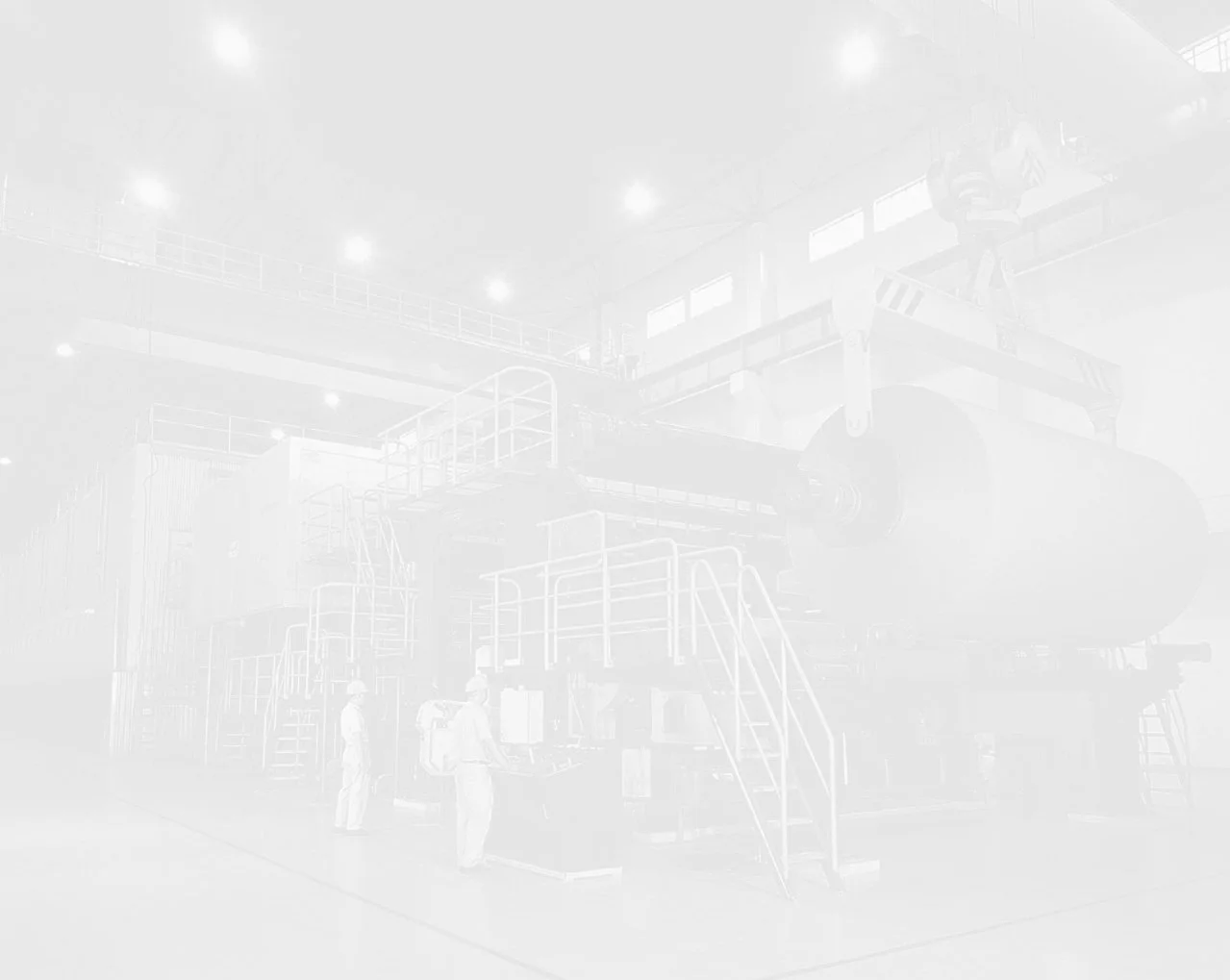
WHAT IS EDGE CRACK Inspection?
Edge cracks are structural weakness points at critical areas of web-based manufacturing processes
This problem effects all grades of paper and when left undiagnosed it will contribute to increased downtime, waste and lower product output
This quality issue will contribute to efficiency decreases at both the parent machine and any downstream value-add systems (converting)
It is essential to develop high ROI solutions to identify this issue
EXISTING SOLUTIONS
Current solutions are costly as they require extensive installation requirements and may require mechanical hardware to allow the edge crack sensor to follow the cross direction (CD) movement of the sheet. Other edge crack detection systems may require the installation of a full cross direction beam of cameras (WIS – web inspection system).
Both of these options involve a wide range of project management requirements and a high long-term cost of ownership. Neither option presents a rapid deployment of the technology.
PAST SOLUTIONS
WIS – WEB INSPECTION SYSTEMS
Camera Based
Limited to installation requirements
In most cases the camera is positioned above the sheet
Cannot be installed on machines that have foils (tissue)
Limited resolution depending on number of cameras and age of system (pixel density)
Cost
Requires extensive infrastructure
Opportunity cost in time to design, install and commission
Capital Project – requires multiple interconnected systems for complete solution
SENSOR BASED WITH MECHANICAL HEAD
Requires mechanical hardware (hydraulics) for sensor to track the edge
No picture of sheet defect – sensor based only
No control room operator interface
Requires close proximity to sheet edge
Requires coverage on both sides of the sheet – will not work with tissue foils
Requires extensive infrastructure: Sensor Head, hydraulics and mounting hardware, separate junction box and connections for break signal
Opportunity cost in time to design, install and commission
Capital Project
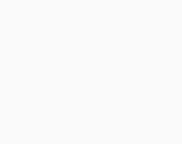
PAST SOLUTIONS have a common theme
Overly complicated
Problem must be extreme for the ROI model to work
This means significant potential loss to the mill as the problem is often times tolerated but not capture and solved